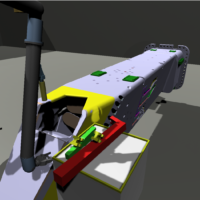
ITER Hands-on maintenance – Virtual Reality simulations
BSc/MSc Student Assignment ITER
Introduction
ITER, “International Thermonuclear Experimental Reactor”, is a large-scale scientific experiment that aims to demonstrate that it is possible to produce commercial energy from fusion. Some parts of the reactor become too “hot” to handle and need to be maintained by hand, which is done remotely.
During ITER maintenance shutdowns, the maintenance crews work for several months in 24/6 shifts, inspecting and replacing worn and broken components, with the purpose to bring the experimental ITER reactor back into an operational state as fast as possible. The level of contamination (with toxic materials) and activation (yielding high dose rates gamma radiation) of Tokamak components imply that many of these maintenance activities have to be done by Remote Handling (RH), using master / slave manipulators, cranes and automated transport containers. The more delicate and precise maintenance operations will be done by dexterous haptic telemanipulation systems.
In order to reduce the maintenance interval, maintenance activities will be performed in parallel at several locations, such as at various levels on the inside of the Tokamak, in the Neutral Beam Hot Cell, in the Cask Transportation System and throughout various work stations in the ITER Hot Cell Facility. All Remote Handling operations are coordinated and controlled from a High-level Control Room. Up to twelve workstations with up to four operators each are foreseen. Each workstation is typically equipped with one or two master arms to directly control dexterous slave manipulators. In order to preserve flexibility in allocating master control stations to specific slave robots, middleware makes it possible to establish flexible real-time connections between different master and slave devices.
Some tasks with lower radiation levels will be handled using hands on maintenance. To make sure that radiation exposure for maintenance personnel is as low as reasonably possible (following the ALARA principle), we analyze the ITER component designs with respect to their compatibility for hands on maintenance. One of the tools used in this process is through a Virtual Reality (VR) Setup. Using a VR we get virtual ‘hands-on’ experience, and thus assess hands-on maintenance procedures in a relative intuitive way.
Project
Do you have experience handling CAD software and models and are you motivated at the prospect of using your engineering skills towards evaluating ITER component designs? HIT is looking for interns/students who are willing to sharpen their engineering skills and support HIT operations related to ITER work. Specifically, you will be providing support in the development of VR simulations towards the critical evaluation of hands-on maintenance at complex systems. In addition, you will support maintenance feasibility assessments of ITER component designs and provide design feedback towards the continued developments of the assessed components.
Expected Output:
- Developed VR hands-on maintenance simulations
- Integration of the the latest VR developments (e.g. VRTK SDK);
- Build standalone executable(s) of a working scene for hands on maintenance;
Requirements:
- Excited about new technologies, eager to work on state-of-the-art technologies;
- Independent, enthusiastic, critical and research-driven;
- Sense of responsibility, duty fulfillment;
- Eager to work in an international environment, team-player, and able to collaborate with multiple organizations and companies;
- Determined to dedicate time to the project, able to set priorities;
- Skilled in documentation and presentation of (intermediate) achieved results;
- Excellent problem-solving skills;
- Knowledge of 3D software (3ds Max and/or SolidWorks are a plus);
- Knowledge of VR software (Unity, VRTK, 3ds max);
- Understanding of programming (C#).
What do we offer?
- International environment;
- Hands-on experience with robotics in the face of real-life challenges;
- State-of-the-art hardware (e.g. haptic simulator, care robot, etc.)
- Bi-weekly progress meetings;
- A daily supervisor to provide guidance if needed.